Todos nuestros fabricados llevan un tratamiento final de galvanizado.
Éste es uno de los acabados que se utilizan para mejorar la resistencia a la corrosión del acero (y las aleaciones de hierro) mediante un pequeño recubrimiento superficial. Éste tipo de solución es muy efectiva incluso en ambientes de elevada corrosión (Véase Tabla 1. Fuente: UNE EN ISO 14713: “Protección frente a la corrosión de las estructuras de hierro y acero mediante recubrimientos de zinc y aluminio. Directrices”).
TABLA 1 | ||
---|---|---|
Corrosividad de las atmósferas y velocidades de corrosión del zinc. | ||
Categoría de corrosividad | Ambientes | Velocidad corrosión del zinc (µm/año) |
C1 | Interior: Seco | Inferior o igual a 0.1 |
C2 | Interior: Condensación ocasional | 0,1 a 0,7 |
Exterior: Rural en el interior del país | 0,1 a 0,7 | |
C3 | Interior: Humedad elevada, aire ligeramente contaminado | 0,7 a 2 |
Exterior: Urbano en el interior del país o costero de baja salinidad | 0,7 a 2 | |
C4 | Interior: Piscinas, plantas químicas, etc. | 2 a 4 |
Exterior: Industrial en el exterior del país o urbano costero | 2 a 4 | |
C5 | Exterior: Industrial muy húmedo o costero de elevada salinidad | 4 a 8 |
El acero desprotegido tiene un promedio de vida de tan solo dos años, antes de que queden afectadas su funcionalidad o su integridad estructural. En cambio, los recubrimientos galvanizados obtenidos en las plantas de galvanizado duran como mínimo diez años sin necesidad de mantenimiento alguno, incluso en las peores condiciones atmosféricas.
La norma básica que especifica las características que deben cumplir los recubrimientos galvanizados que se obtienen en las instalaciones discontinuas de galvanización en caliente, es la norma española e internacional UNE EN ISO 1461, “Recubrimientos galvanizados en caliente sobre productos acabados de hierro y acero”.
El galvanizado consiste en la formación de un recubrimiento de zinc sobre las piezas y productos de hierro o acero mediante inmersión de los mismos en un baño de zinc fundido a 450ºC.
Durante la inmersión en el zinc fundido, se produce una reacción de difusión entre el zinc y el acero que tiene como resultado la formación de diferentes capas de aleaciones zinc-hierro.
Cuando se extraen los materiales del baño de zinc, dichas capas de aleación quedan cubiertas por una capa externa del metal en estado puro, las cuales, en conjunto, le confieren al acero una excelente resistencia a la corrosión.
La reacción de galvanización solamente se produce si las superficies de los materiales están químicamente limpias, por lo que éstos deben someterse previamente a un proceso de preparación superficial.
Por este motivo, los pasos que seguimos en nuestra planta para obtener un correcto acabado superficial son los siguientes:
1-Cuelgue de piezas
2- Desengrasado
3- Decapado
4- Fluxado
5- Galvanizado
6- Descuelgue de pieza
7- Repasado
Las dimensiones de nuestro crisol de galvanizado son de 12,5 m de longitud por 2,5 m de profundidad por 1,5 m de ancho, medidas que nos permiten galvanizar materiales de diversas longitudes y sin apenas limitaciones.
Después de galvanizar las piezas, las sometemos a un proceso de inspección en el cual se evalúa su aspecto final y también el espesor de recubrimiento obtenido, para verificar que cumplan la norma UNE EN ISO 1461.
( Véase Tabla 2).
TABLA 2 | ||
---|---|---|
Espesores mínimos del recubrimiento sobre muestras sin centrifugar Norma UNE EN ISO 1461:2009 | ||
Espesor pieza (mm) | Espesor local mínimo recubrimiento (µm) | Espesor mínimo recubrimiento (µm) |
Acero > 6mm. | 70 | 85 |
Acero > 3mm. hasta ≤ 6 mm. | 55 | 70 |
Acero ≥ 1,5mm. hasta ≤ 3mm. | 45 | 55 |
Acero < 1,5 mm. | 35 | 45 |
Piezas moldeadas ≥ 6mm. | 70 | 80 |
Acero < 6mm. | 60 | 70 |
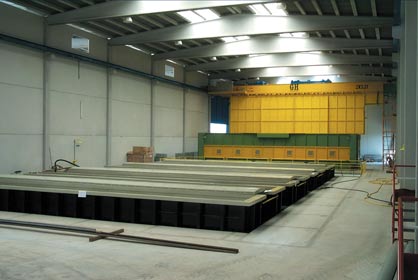
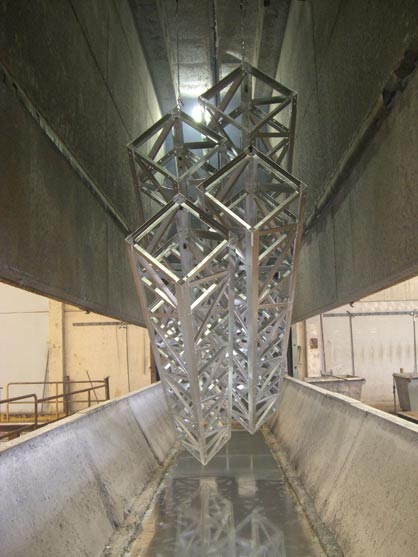
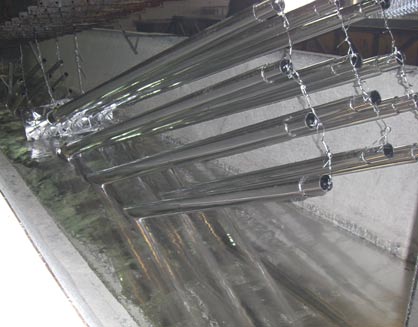
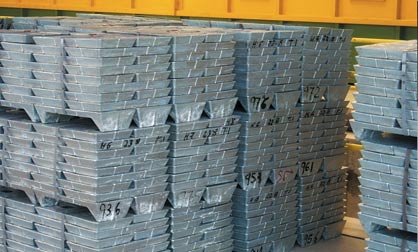